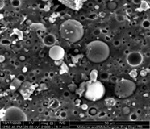
The Effect of Additional Pineapple (Ananas comosus L. Merr.) Peel Pectin on the Characteristics of Coal Fly Ash Geopolymer
Abstract
Fly ash-based geopolymer concrete is a candidate for a more sustainable material than concrete, with lower embodied energy and high early-age compressive strength properties. This work has focused on studying the use of pineapple peel pectin as an additive to enhance the compressive and split tensile strength achievable in a geopolymerization process. The compressive strength and split tensile strength were tested by physical testing, and the mineral phases, functional groups, and microstructure were analyzed by chemical analysis (XRD, FTIR, and SEM-EDX). Geopolymers containing 0%, 1%, and 2.5% pectin were fabricated. The surprising optimum was the 1% variation, which reached compressive strength of 22.13 MPa and split tensile strength of 3.18 MPa when making medium-quality concrete. XRD results of the best performing 1% sample exhibited mainly an amorphous phase, where amorphization is evident at 20–40°2θ due to broad signal peaks, a sign of successful geolypolimerization. Geopolymerization was also confirmed by FTIR analysis through the presence of Si–O–Si and Si–O–Al asymmetric stretching vibration peaks at 1018.41 cm−1, illustrating the inclusion of pectin observed by the C–H stretches in the range 2900–2300 cm−1 and the carboxyl group stretch at 1635.64 cm−1. The microstructure of the quality concrete 1% formulation was characterized by a tight, perfect structure as seen through SEM images, while the 0% and 2.5% mixes had more porous and cracked structures. These results suggest that 1% pectin incorporation improves geopolymer mechanical performance without adversely affecting structure, merits for further mechanical properties, and long-term stability.
Keywords
Full Text:
PDFReferences
[1] M. Ser, A. E. Hussin, A. Said, and M. Kohail, "Advancing sustainable production of eco-friendly foamed concrete: A comprehensive review on utilising waste materials for cement reduction," in 2023 2nd International Conference on Smart Cities 4.0 (Smart Cities 4.0 2023), 2023, pp. 35–40, doi: 10.1109/SmartCities4.056956.2023.10526184.
[2] A. A. Shubbar, D. Al-Jumeily, A. J. Aljaaf, M. Alyafei, M. Sadique, and J. Mustafina, "Investigating the mechanical and durability performance of cement mortar incorporated modified fly ash and ground granulated blast furnace slag as cement replacement materials," in Proceedings - International Conference on Developments in eSystems Engineering (DeSE), 2019, pp. 434–439, doi: 10.1109/DeSE.2019.00086.
[3] R. A. Nevel, R. D. Kumar, and M. Surendar, Review on partially replacement of cement with industrial waste in manufacturing of concrete and bricks, vol. 388, 2024, doi: 10.1007/978-981-99-6233-4_12.
[4] S. A. Miller, V. M. John, S. A. Pacca, and A. Horvath, "Carbon dioxide reduction potential in the global cement industry by 2050," Cement and Concrete Research, vol. 114, pp. 115–124, 2018, doi: 10.1016/j.cemconres.2017.08.026.
[5] G. Habert et al., "Environmental impacts and decarbonisation strategies in the cement and concrete industries," Nature Reviews Earth & Environment, vol. 1, no. 11, pp. 559–573, 2020, doi: 10.1038/s43017-020-0093-3.
[6] B. M. Nejad, S. Enferadi, and R. Andrew, "A comprehensive analysis of process-related CO₂ emissions from Iran’s cement industry," Cleaner Environmental Systems, vol. 16, 2025, doi: 10.1016/j.cesys.2024.100251.
[7] J. Abdayem, G. Aouad, and M. Saba, "Environmental impact assessment of industrial waste geopolymer material," in E3S Web of Conferences, 2024, doi: 10.1051/e3sconf/202458507002.
[8] A. Mushtaq, S. Ali, A. H. Chaudhry, N. Sial, M. Aslam, and H. Batool, "Geopolymers as supplementary cementitious materials to reduce carbon dioxide emissions," Nature Environment and Pollution Technology, vol. 24, pp. 417–429, 2025, doi: 10.46488/NEPT.2025.v24iS1.000.
[9] N. R. Kadhim, A. T. Abdulrasool, and S. S. Mohammed, "Cementitious materials of waste used in the production of geopolymer concrete: An overview," in AIP Conference Proceedings, 2023, doi: 10.1063/5.0121599.
[10] K. Goryunova, Y. Gahramanli, V. Muradkhanli, and P. Nadirov, "Phosphate-activated geopolymers: Advantages and application," RSC Advances, vol. 13, 43, pp. 30329–30345, 2023, doi: 10.1039/d3ra05131e.
[11] S. V. S. Shankari and M. Sivasakthi, "A state-of-the-art review on effectiveness of geopolymer technology toward dye degradation, heavy metal encapsulation and its prospects on environmental remediation," Environmental Quality Management, vol. 34, no. 3, 2025, doi: 10.1002/tqem.70054.
[12] K. Wang and H. Le, "The development of cement-based, intumescent and geopolymer fire-retardation coatings for metal structures: A review," Coatings, vol. 13, no. 3, 2023, doi: 10.3390/coatings13030495.
[13] S. Mustafa, M. A. Hameed, and A. Dulaimi, "Eco-friendly geopolymer concrete: A critical review," in AIP Conference Proceedings, 2023, doi: 10.1063/5.0163551.
[14] S. Luhar, I. Luhar, and R. Gupta, "Durability performance evaluation of green geopolymer concrete," European Journal of Environmental and Civil Engineering, vol. 26, no. 10, pp. 4297–4345, 2022, doi: 10.1080/19648189.2020.1847691.
[15] K. Dhasindrakrishna, K. Pasupathy, S. Ramakrishnan, and J. Sanjayan, "Progress, current thinking and challenges in geopolymer foam concrete technology," Cement and Concrete Composites, vol. 116, 2021, doi: 10.1016/j.cemconcomp.2020.103886.
[16] T. S. Alahmari, T. A. Abdalla, and M. A. M. Rihan, "Review of recent developments regarding the durability performance of eco-friendly geopolymer concrete," Buildings, vol. 13, no. 12, 2023, doi: 10.3390/buildings13123033.
[17] S. Sbahieh, G. McKay, and S. G. Al-Ghamdi, "Comprehensive analysis of geopolymer materials: Properties, environmental impacts, and applications," Materials, vol. 16, no. 23, 2023, doi: 10.3390/ma16237363.
[18] L. N. Assi, A. Alsalman, R. S. Kareem, K. Carter, and J. Khatib, Mechanical and durability properties of sustainable geopolymer concrete, 2024, doi: 10.1016/B978-0-443-15672-4.00004-8.
[19] C. Gowthamaraj and G. Vimalanandan, Effect of steel fibre and plastering sand on GGBS and silica fume based geo-polymer concrete, vol. 387, 2024, doi: 10.1007/978-981-99-6175-7_35.
[20] H. U. Ahmed et al., "Compressive strength of sustainable geopolymer concrete composites: A state-of-the-art review," Sustainability (Switzerland), vol. 13, no. 24, 2021, doi: 10.3390/su132413502.
[21] M. A. M. Rihan, R. O. Onchiri, N. Gathimba, and B. Sabuni, "Mix design approaches of eco-friendly geopolymer concrete: A critical review," Hybrid Advances, vol. 7, 2024, doi: 10.1016/j.hybadv.2024.100290.
[22] M. Matsuoka, K. Yokoyama, K. Okura, N. Murayama, M. Ueda, and M. Naito, "Synthesis of geopolymers from mechanically activated coal fly ash and improvement of their mechanical properties," Minerals, vol. 9, no. 12, 2019, doi: 10.3390/min9120791.
[23] N. Li et al., "Mechanical activation of fly ash: Effect on performance and mechanism of resulting geopolymer," Journal of Functional Materials, vol. 49, no. 4, pp. 04102–04106, 2018, doi: 10.3969/j.issn.1001-9731.2018.04.018.
[24] P. Sukmak, S. Horpibulsuk, and S.-L. Shen, "Strength development in clay-fly ash geopolymer," Construction and Building Materials, vol. 40, pp. 566–574, 2013, doi: 10.1016/j.conbuildmat.2012.11.015.
[25] M. Khawaji, "Hydration, microstructure, and properties of fly ash-based geopolymer: A review," Materials Science-Poland, vol. 41, no. 2, pp. 263–287, 2023, doi: 10.2478/msp-2023-0006.
[26] P. Bhardwaj, R. Gupta, S. T. Salammal, C. Dhand, and D. Mishra, "Recent trends in mechanochemical processing of fly ash aluminosilicate materials (geopolymers): Advancement, challenges, and opportunities," Journal of Material Cycles and Waste Management, vol. 26, no. 1, pp. 1–19, 2024, doi: 10.1007/s10163-023-01817-2.
[27] K. Zarębska, J. Szczurowski, J. Muszyńska, and P. Baran, "Geopolymer materials from fly ash—A sustainable approach to hazardous waste management," Materials, vol. 17, no. 14, 2024, doi: 10.3390/ma17143515.
[28] K. M. Zierold and C. Odoh, "A review on fly ash from coal-fired power plants: Chemical composition, regulations, and health evidence," Reviews on Environmental Health, vol. 35, no. 4, pp. 401–418, 2020, doi: 10.1515/reveh-2019-0039.
[29] S. Z. Naqvi, J. Ramkumar, and K. K. Kar, Functionalization of fly ash, 2021, doi: 10.1016/B978-0-12-817686-3.00012-8.
[30] X. Chao, T.-A. Zhang, G. Lv, Q. Zhao, F. Cheng, and Y. Guo, "Sustainable application of coal fly ash: One-step hydrothermal cleaner production of silicon-potassium mineral fertilizer synergistic alumina extraction," Journal of Cleaner Production, vol. 426, 2023, doi: 10.1016/j.jclepro.2023.139110.
[31] Y. Luna-Galiano, C. Fernández-Pereira, and M. Izquierdo, "Contributions to the study of porosity in fly ash-based geopolymers: Relationship between degree of reaction, porosity and compressive strength," Materiales de Construcción, vol. 66, no. 324, 2016, doi: 10.3989/mc.2016.10215.
[32] M. A. Sultan, Imran, and F. Litiloly, "Correlation of concrete porosity with average compressive strength," Journal of Civil Technology,” vol. 2, no. 2, pp. 61–68, 2018.
[33] Yanuar, E. Kusumastuti, and Jumaeri, "Synthesis and characterization of geopolymer with the addition of water hyacinth fiber and aluminum powder," Indonesian Journal of Chemical Science, vol. 6, no. 3, 2017.
[34] N. A. Mohd Mortar, H. Kamarudin, R. A. Rafiza, T. A. F. Meor, and M. Rosnita, "Compressive strength of fly ash geopolymer concrete by varying sodium hydroxide molarity and aggregate to binder ratio," in IOP Conference Series: Materials Science and Engineering, IOP Publishing Ltd, Jul. 2020, doi: 10.1088/1757-899X/864/1/012037.
[35] S. Samantasinghar and S. P. Singh, "Effect of synthesis parameters on compressive strength of fly ash-slag blended geopolymer," Construction and Building Materials, vol. 170, pp. 225–234, 2018, doi: 10.1016/j.conbuildmat.2018.03.026.
[36] Y. Patrisia, R. Coenraad, N. A. Inderawan, and E. Elidad, "Mechanical properties of fly ash-based geopolymer concrete using variation in maximum size of coarse aggregate," in Journal of Physics: Conference Series, Institute of Physics Publishing, Feb. 2020, doi: 10.1088/1742-6596/1469/1/012025.
[37] U. Rattanasak, K. Pankhet, and P. Chindaprasirt, "Effect of chemical admixtures on properties of high-calcium fly ash geopolymer," International Journal of Minerals, Metallurgy and Materials, vol. 18, no. 3, pp. 364–369, 2011, doi: 10.1007/s12613-011-0448-3.
[38] C. Rahmawati et al., "Mechanical properties and fracture parameters of geopolymers based on cellulose nanocrystals from Typha sp. fibers," Case Studies in Construction Materials, vol. 17, 2022, doi: 10.1016/j.cscm.2022.e01498.
[39] H. Ye, Y. Zhang, Z. Yu, and J. Mu, "Effects of cellulose, hemicellulose, and lignin on the morphology and mechanical properties of metakaolin-based geopolymer," Construction and Building Materials, vol. 173, pp. 10–16, 2018, doi: 10.1016/j.conbuildmat.2018.04.028.
[40] C. Lv, J. Liu, G. Guo, and Y. Zhang, "The mechanical properties of plant fiber-reinforced geopolymers: A review," Polymers (Basel), vol. 14, no. 19, 2022, doi: 10.3390/polym14194134.
[41] M. Jin, L. Chen, L. Chen, and Z. Jin, "Compressive strength and SEM observations of geopolymers reinforced by carbon fibers, polyacrylonitrile fibers and cellulose fibers," Advanced Materials Research, vol. 472–475, pp. 570–575, 2012, doi: 10.4028/www.scientific.net/AMR.472-475.570.
[42] Hisan, E. Kusumastuti, and W. Mahatmanti, "Utilization of pineapple leaf fibers in the synthesis of coal fly ash-based geopolymers," Indonesian Journal of Chemical Science, vol. 6, no. 2, 2017.
[43] Anwar and E. Kusumastuti, "Utilization of banana tree fibers in the synthesis of coal fly ash geopolymer," Indonesian Journal of Chemical Science, vol. 5, no. 1, pp. 1–65, 2016.
[44] L. Yi et al., "Source, extraction, properties, and multifunctional applications of pectin: A short review," Polymers (Basel), vol. 16, no. 20, 2024, doi: 10.3390/polym16202883.
[45] D. Jat, R. Motiani, S. Dalal, and I. Thakar, "Mechanical properties of geopolymer concrete reinforced with various fibers: A review," vol. 294, 2023, doi: 10.1007/978-981-19-6297-4_11.
[46] R. Karim, M. B. Uddin, and M. F. Jubayer, "Optimization of pectin isolation method from pineapple (Ananas comosus L.) waste," Carpathian Journal of Food Science and Technology, vol. 6, no. 2, pp. 116–122, 2014.
[47] N. A. Zakaria et al., "Extraction optimization and physicochemical properties of high methoxyl pectin from Ananas comosus peel using microwave-assisted approach," Journal of Food Measurement and Characterization, vol. 17, no. 4, pp. 3354–3367, 2023, doi: 10.1007/s11694-023-01858-z.
[48] M. Lumbanraja et al., "Microwave-assisted extraction and characterisation of pectin from pineapple biomass," in AIP Conference Proceedings, 2023, doi: 10.1063/5.0116775.
[49] O. H. Ahmed, M. H. Husni, A. R. Anuar, and M. M. Hanafi, "Towards sustainable use of potassium in pineapple waste," The Scientific World Journal, vol. 4, pp. 1007–1013, 2004, doi: 10.1100/tsw.2004.199.
[50] A. H. Nu’Man, L. Nurwandi, I. Bahtiar, and S. Omar, “Pineapple peel industry determination with weighted location method,” in IOP Conference Series: Materials Science and Engineering, 2020. doi: 10.1088/1757-899X/830/3/032099.
[51] J. T. Casabar, R. Ramaraj, S. Tipnee, and Y. Unpaprom, “Enhancement of hydrolysis with Trichoderma harzianum for bioethanol production of sonicated pineapple fruit peel,” Fuel, vol. 279, 2020, doi: 10.1016/j.fuel.2020.118437.
[52] A. Zziwa, J. Jjagwe, S. Kizito, I. Kabenge, A. J. Komakech, and H. Kayondo, “Nutrient recovery from pineapple waste through controlled batch and continuous vermicomposting systems,” J Environ Manage, vol. 279, 2021, doi: 10.1016/j.jenvman.2020.111784.
[53] S. A. M. Sukri et al., “Pineapple waste in animal feed: A review of nutritional potential, impact and prospects,” Annals of Animal Science, vol. 23, no. 2, pp. 339–352, 2023, doi: 10.2478/aoas-2022-0080.
[54] J. A. T. Linhares et al., Study of the Properties of Geopolymeric Mortars with the Addition of Natural Pineapple Fibers in the Fresh State. 2023. doi: 10.1007/978-3-031-22576-5_59.
[55] A. Karthik, K. Sudalaimani, C. T. Vijayakumar, and S. S. Saravanakumar, “Effect of bio-additives on physico-chemical properties of fly ash-ground granulated blast furnace slag based self cured geopolymer mortars,” J Hazard Mater, vol. 361, pp. 56–63, 2019, doi: 10.1016/j.jhazmat.2018.08.078.
[56] P. H. F. Pereira et al., “Effect of the chemical treatment sequence on pineapple peel fiber: chemical composition and thermal degradation behavior,” Cellulose, vol. 29, no. 16, pp. 8587–8598, 2022, doi: 10.1007/s10570-022-04806-0.
[57] M. Mehraj et al., “Nutritional Composition and Therapeutic Potential of Pineapple Peel – A Comprehensive Review,” Chem Biodivers, vol. 21, no. 5, 2024, doi: 10.1002/cbdv.202400315.
[58] G. O. Coelho, I. Deleris, D. Champion, J. Wallecan, S. Debon, and G. Roudaut, “Multiscale dynamics and molecular mobility in cellulose-rich materials,” Carbohydr Polym, vol. 344, 2024, doi: 10.1016/j.carbpol.2024.122490.
[59] M. M. Camargo, E. A. Taye, J. A. Roether, D. T. Redda, and A. R. Boccaccini, “A review on natural fiber-reinforced geopolymer and cement-based composites,” Materials, vol. 13, no. 20, pp. 1–29, 2020, doi: 10.3390/ma13204603.
[60] N. A. Al-Ghazali, F. N. A. A. Aziz, K. Abdan, and N. A. M. Nasir, “Mechanical Properties of Natural Fibre Reinforced Geopolymer Composites: A Review,” Pertanika J Sci Technol, vol. 30, no. 3, pp. 2053–2069, 2022, doi: 10.47836/pjst.30.3.16.
[61] N. S. Amalia, S. Syamsidar, A. Haris, and Subaer, “Physico-mechanics properties of hybrid composite geopolymers-pineapple leaf fiber (PLF),” in AIP Conference Proceedings, 2018. doi: 10.1063/1.5066815.
[62] J. A. T. Linhares et al., Characterization and Mechanical Behavior of Pineapple Fiber Reinforced Geopolymer Composites. 2023. doi: 10.1007/978-3-031-22576-5_25.
[63] J. Luo et al., “Improving the gel properties of Ficus pumila Linn. pectin by incorporating deacetylated konjac glucomannan,” Int J Biol Macromol, vol. 278, 2024, doi: 10.1016/j.ijbiomac.2024.134985.
[64] A. Nawaz et al., “Effect of structurally different pectin on dough rheology, structure, pasting and water distribution properties of partially meat-based sugar snap cookies,” Foods, vol. 10, no. 11, 2021, doi: 10.3390/foods10112692.
[65] A. Lapomarda et al., “Pectin as rheology modifier of a gelatin-based biomaterial ink,” Materials, vol. 14, no. 11, 2021, doi: 10.3390/ma14113109.
[66] G. G. Zampar, I. C. Zampar, S. Beserra da Silva de Souza, C. da Silva, and B. C. Bolanho Barros, “Effect of solvent mixtures on the ultrasound-assisted extraction of compounds from pineapple by-product,” Food Biosci, vol. 50, 2022, doi: 10.1016/j.fbio.2022.102098.
[67] F. de Andrade Maia and L. H. Fasolin, “Recovery of bioactive compounds from pineapple waste through high-pressure technologies,” Journal of Supercritical Fluids, vol. 218, 2025, doi: 10.1016/j.supflu.2024.106455.
[68] D. N. A. Zaidel, N. N. Zainudin, Y. M. M. Jusoh, and I. I. Muhamad, “Extraction and characterisation of pectin from sweet potato (Ipomoea batatas) pulp,” Journal of Engineering Science and Technology, vol. 10, no. Spec.issue, pp. 22–29, 2015.
[69] M. Ccencho, V. Quijada, and L. Vinces, An Automated System for the Stage of Hydrolysis and Filtration in the Extraction of Pectin from the Cocoa Shell, vol. 202. 2021. doi: 10.1007/978-3-030-57566-3_26.
[70] Antika and Kurniawati, “Isolation and Characterization of Pectin from Pineapple Peel,” in Proceedings of the National Seminar on Chemistry FMIPA UNESA, 2017.
[71] D. K. Sari, E. P. Setyaningsih, H. Fansuri, and T. E. Susanto, “Kajian Karakteristik Kimia dan Fisika Abu Layang yang Menjadi Penentu Kekuatan Mekanik Perekat Geopolimer Berbahan Dasar Abu Layang,” Akta Kimia Indonesia, vol. 3, no. 2, p. 222, Dec. 2018, doi: 10.12962/j25493736.v3i2.4563.
[72] S. Bespalko, O. Halychyi, M. Roha, S. Poliakov, G. Kaleinikov, and T. Naumenko, “Experimental Study of the Thermal Effect of the Dissolution Reaction for Some Alkalis and Salts with Natural Mixing and Forced Stirring,” in E3S Web of Conferences, 2019. doi: 10.1051/e3sconf/201911801026.
[73] O. Shee-Ween et al., “Cold-pressed fly ash geopolymers: effect of formulation on mechanical and morphological characteristics,” Journal of Materials Research and Technology, vol. 15, pp. 3028–3046, 2021, doi: 10.1016/j.jmrt.2021.09.084.
[74] F. Li et al., “Fly-ash-based geopolymer modified by metakaolin for greener grouting material,” Proceedings of the Institution of Civil Engineers: Engineering Sustainability, vol. 177, no. 3, pp. 125–138, 2023, doi: 10.1680/jensu.22.00079.
[75] M. Chi, “Effects of the alkaline solution/binder ratio and curing condition on the mechanical properties of alkali-activated fly ash mortars,” Science and Engineering of Composite Materials, vol. 24, no. 5, pp. 773–782, 2017, doi: 10.1515/secm-2015-0305.
[76] E. Sitarz-Palczak, J. Kalembkiewicz, and D. Galas, “Comparative study on the characteristics of coal fly ash and biomass ash geopolymers,” Archives of Environmental Protection, vol. 45, no. 1, pp. 126–135, 2019, doi: 10.24425/aep.2019.126427.
[77] ASTM C-618-03, “Standard Specification for Coal Fly Ash and Raw or Calcined Natural Pozzolan for Use,” Annual Book of ASTM Standards, vol. 04, no. C, pp. 3–6, 2003.
[78] A. Wongkvanklom, V. Sata, J. G. Sanjayan, and P. Chindaprasirt, “Setting time, compressive strength and sulfuric acid resistance of a high calcium fly ash geopolymer containing borax,” Engineering and Applied Science Research, vol. 45, no. 2, pp. 89–94, 2018, doi: 10.14456/easr.2018.20.
[79] Y. Li, Y. Dong, M. R. El-Naggar, F. Wang, and Y. Zhao, “The Influence of Particle Size and Calcium Content on Performance Characteristics of Metakaolin- and Fly-Ash-Based Geopolymer Gels,” Gels, vol. 10, no. 10, 2024, doi: 10.3390/gels10100639.
[80] X. Ge, X. Hu, and C. Shi, “The effect of different types of class F fly ashes on the mechanical properties of geopolymers cured at ambient environment,” Cem Concr Compos, vol. 130, 2022, doi: 10.1016/j.cemconcomp.2022.104528.
[81] X. Ge, X. Hu, and C. Shi, “Impact of micro characteristics on the formation of high-strength Class F fly ash-based geopolymers cured at ambient conditions,” Constr Build Mater, vol. 352, 2022, doi: 10.1016/j.conbuildmat.2022.129074.
[82] H. Fansuri, D. Prasetyoko, Z. Zhang, and D. Zhang, “The effect of sodium silicate and sodium hydroxide on the strength of aggregates made from coal fly ash using the geopolymerisation method,” Asia-Pacific Journal of Chemical Engineering, vol. 7, no. 1, pp. 73–79, 2012, doi: 10.1002/apj.493.
[83] H. Pan et al., “Dynamic compressive behavior of high-strength engineered geopolymer composites,” Journal of Building Engineering, vol. 80, 2023, doi: 10.1016/j.jobe.2023.108036.
[84] H. Kasyanto, “Tinjauan Kuat Tekan Geopolimer Berbahan Dasar Fly Ash dengan Aktivator Sodium Hidroksida dan Sodium Silikat,” Industrial Research Workshop and National Seminar, vol. 3, pp. 254–259, 2012.
[85] N. Amalia, S. Hidayatullah, Nurfadilla, and Subaer, “The mechanical properties and microstructure characters of hybrid composite geopolymers-pineapple fiber leaves (PFL),” in IOP Conference Series: Materials Science and Engineering, 2017. doi: 10.1088/1757-899X/180/1/012012.
[86] A. E. Irudayaraj, A. Veerabathiran, R. A. Raj, and D. A. Prabu, “Synthesis and characterization of pectin biopolymer from orange peel wastes and its effect on pineapple fiber-reinforced vinyl ester composite,” Biomass Convers Biorefin, vol. 15, no. 1, pp. 1609–1620, 2025, doi: 10.1007/s13399-024-06245-2.
[87] R. Zulfiati, Saloma, and Y. Idris, “Mechanical Properties of Fly Ash-Based Geopolymer with Natural Fiber,” in Journal of Physics: Conference Series, 2019. doi: 10.1088/1742-6596/1198/8/082021.
[88] M. C. Conceição, T. N. Fernandes, M. E. T. Prado, and J. V. de Resende, “Effect of sucrose and pectin addition on physical, chemical, thermal and rheological properties of frozen/thawed pineapple pulps,” Korea Australia Rheology Journal, vol. 24, no. 3, pp. 229–239, 2012, doi: 10.1007/s13367-012-0028-8.
[89] E. Kusumastuti, “Utilization of Mount Merapi Volcanic Ash as Geopolymer (an inorganic aluminosilicate polymer),” Unnes Journal of MIPA, vol. 35, no. 1, pp. 67–76, 2012.
[90] X. Tian, W. Xu, S. Song, F. Rao, and L. Xia, “Effects of curing temperature on the compressive strength and microstructure of copper tailing-based geopolymers,” Chemosphere, vol. 253, 2020, doi: 10.1016/j.chemosphere.2020.126754.
[91] H. Thuilliez, C. Lanos, A. Phelipot-Mardelé, and G. Mauvoisin, Interaction Between Drying Shrinkage and Hardening of Geopolymers, vol. 482 LNCE. 2024. doi: 10.1007/978-981-97-1972-3_52.
[92] J. Latupeirissa, E. G. Fransina, M. F. J. D. P. Tanasale, and C. Y. Batawi, “EKSTRAKSI DAN KARAKTERISASI PEKTIN KULIT JERUK MANIS KISAR (Citrus sp.) Extraction and Characterization Of Pectin From The Oranges Peel Of Kisar (Citrus sp.),” Indonesian Journal of Chemical Research, vol. 7, pp. 53-60, 2019, doi: 10.30598//ijcr.2019.7-egf.
[93] Y. Zhang, J. Zhang, J. Jiang, D. Hou, and J. Zhang, “The effect of water molecules on the structure, dynamics, and mechanical properties of sodium aluminosilicate hydrate (NASH) gel: A molecular dynamics study,” Constr Build Mater, vol. 193, pp. 491–500, 2018, doi: 10.1016/j.conbuildmat.2018.10.221.
[94] D. Hou et al., “Molecular Insight into the Formation and Fracture Process of Sodium Aluminosilicate Hydrate Gels,” Journal of Physical Chemistry C, vol. 127, no. 31, pp. 15542–15555, 2023, doi: 10.1021/acs.jpcc.3c02632.
[95] N. S. Amalia, S. Syamsidar, A. Haris, and Subaer, “Physico-mechanics properties of hybrid composite geopolymers-pineapple leaf fiber (PLF),” in AIP Conference Proceedings, 2018. doi: 10.1063/1.5066815.
[96] J. Liu and C. Lv, “Durability of Cellulosic-Fiber-Reinforced Geopolymers: A Review,” Molecules, vol. 27, no. 3, 2022, doi: 10.3390/molecules27030796.
[97] X. Guan, M. Xu, B. Li, and H. Do, “Interactions between Amorphous Silica and Sodium Alumino-Silicate Hydrate Gels: Insight from Reactive Molecular Dynamics Simulation,” Journal of Physical Chemistry C, vol. 127, no. 27, pp. 13302–13316, 2023, doi: 10.1021/acs.jpcc.3c02462.
[98] Z. Ma et al., “Long-term dissolution behavior of amorphous aluminosilicate in sodium hydroxide solution for geopolymer synthesis using circulating fluidized bed combustion fly ash,” Constr Build Mater, vol. 394, 2023, doi: 10.1016/j.conbuildmat.2023.132143.
[99] S. Anwar and E. Kusumastuti, “Pemanfaatan Serat Pohon Pisang Dalam Sintesis Geopolimer Abu Layang Batubara,” Indonesian Journal of Chemical Science, vol. 5, no. 1, pp. 1–6, 2016.
[100] A. E. Irudayaraj, A. Veerabathiran, R. A. Raj, and D. A. Prabu, “Synthesis and characterization of pectin biopolymer from orange peel wastes and its effect on pineapple fiber-reinforced vinyl ester composite,” Biomass Convers Biorefin, vol. 15, no. 1, pp. 1609–1620, 2025, doi: 10.1007/s13399-024-06245-2.
[101] R. Zulfiati, Saloma, and Y. Idris, “Mechanical Properties of Fly Ash-Based Geopolymer with Natural Fiber,” in Journal of Physics: Conference Series, 2019. doi: 10.1088/1742-6596/1198/8/082021.
[102] D. Das and P. K. Rout, “Synthesis, Characterization and Properties of Fly Ash Based Geopolymer Materials,” J Mater Eng Perform, vol. 30, no. 5, pp. 3213–3231, May 2021, doi: 10.1007/s11665-021-05647-x.
[103] E. Álvarez-Ayuso et al., “Environmental, physical and structural characterisation of geopolymer matrixes synthesised from coal (co-)combustion fly ashes,” J Hazard Mater, vol. 154, no. 1–3, pp. 175–183, 2008, doi: 10.1016/j.jhazmat.2007.10.008.
[104] H. Chkala, I. Kirm, S. Ighir, A. Ourmiche, M. Chigr, and N. E. El Mansouri, “Preparation and characterization of eco-friendly composite based on geopolymer and reinforced with date palm fiber,” Arabian Journal of Chemistry, vol. 17, no. 2, Feb. 2024, doi: 10.1016/j.arabjc.2023.105510.
[105] W. Schmidt, H. J. H. Brouwers, H. C. Kühne, and B. Meng, “Interactions of polysaccharide stabilising agents with early cement hydration without and in the presence of superplasticizers,” Constr Build Mater, vol. 139, pp. 584–593, May 2017, doi: 10.1016/j.conbuildmat.2016.11.022.
[106] M. Karthe and M. Balakrishnan, “Influence of Silanized Pectin Derived from Dragon Fruit Peel and its Toughening Effect on Pineapple Fibre-Vinyl Ester Composite Subjected to Accelerated Aging,” Silicon, vol. 16, no. 12, pp. 5109–5120, 2024, doi: 10.1007/s12633-024-03073-x.
Refbacks
- There are currently no refbacks.